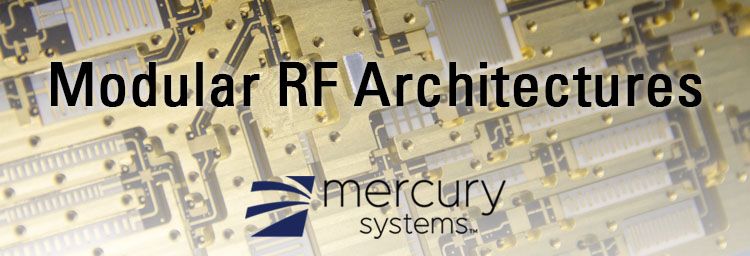
Modular RF Architectures
Mario LaMarche
June 12, 2018
Let’s start with the traditional approach. After spending the morning helping production with some tuning on an amplifier, you finally start reading through the 120-page RFP, SCD, and SOW for the new up-converter. At the end of the source control drawing there is an oddly shaped mechanical outline. The control signal is routed through a hermetic micro-D connector with a custom defined pin-out. While not ideal, the locations of the RF ports are manageable. The eight-month timeline to CDR appears reasonable. However, six months in and it becomes clear that it will take longer and cost more than anticipated. The back and forth iterations with the engineer supporting the custom designed digital control board seem to go on forever. The engineer working on the output module determines that she will need a new heat-sink to keep the devices from becoming too hot. The mixer is generating a spur that wasn’t predicted and somewhere a gain stage is oscillating. The frustrated program manager has to add this project to the long list of development jobs with irate customers.
In my first post in this series on the intersection of the RF commercial industry and the RF defense industry I discussed the critical need for innovative engineering teams. In this second post we will explore a specific technology that enabled rapid growth in the commercial industry and is now emerging in the defense industry—standards and modular architectures. Just as commercial communication standards fueled rapid growth by allowing the re-use of modular components, disruptive RF companies are now working to apply these same methods to the defense industry. However, to be successful is no easy task. With a much smaller available market, these innovative companies require a thorough understanding of current and future market trends in order to define their technology road-map.
Returning to the example above, when every element of an integrated product is designed from scratch the opportunities for problems increase dramatically. All it takes is one unstable amplifier, an out-of-tolerance PCB or a voltage regulator that can’t handle the current.
One minor oversight, out-of-spec component or delay receiving material can delay the entire project and when there are multiple issues all occurring at once the schedule and cost impact can be nearly impossible to predict. As complexity increases, the interface between the different sub-assemblies also becomes critical. Standard or low voltage TTL? Will the silver plated filter create a galvanic reaction when placed against the nickel plated SSPA?
A Lesson from Commercial Technology
An example of the opposite extreme is currently sitting in front of me on my desk. For less than $100 an Arduino board has significant capability. How is the price so low and how do they keep coming out with new versions so quickly? By not re-inventing the wheel. Instead of a custom designed RF front-end, a packaged wifi module is included that lets me control it with my phone. Since the wifi module complies with the IEEE 802.11 standard, I can trust that the dynamic range is sufficient, that the current draw is acceptable, and that the chip will support the modulation requirements. A similar concept applies to the microcontroller.
Obviously a complex EW transceiver can’t use the same components as an Arduino, but there is opportunity to take a page from the commercial industry's playbook—through the use of design re-use and common standards cost, lead-time and risk can be greatly reduced.
Design re-use is not new. Nearly all engineers will look for the opportunity to reuse portions of old designs. However, as a company grows and develops a broad product portfolio, it becomes critical how the design blocks are preserved and also how the various engineers interact with each other. In order to utilize a design library there must be a culture of collaboration. Additionally, in order to get the most value out of re-use, the building blocks must contain innovative technology—there is no point to a library of poorly designed blocks. By amortizing the cost of these innovations across multiple products the full benefit of technology re-use is achieved.
RF Standards for the Defense Industry
The use of standards in the defense and aerospace industries is less common but very effective. As an example we can look to OpenVPX. Understanding the need for such a standard, Mercury Systems led the development and implementation of OpenVPX, which defines the module-to-module and module-to-backplane interfaces allowing for easy interoperability. Instead of a design from scratch, an OpenVPX design provides a framework to simplify both the design and integration into the next higher assembly.
While industry standards improve interoperability between products, internal standards reduce the technical risks in a complex product development. For example, to rapidly develop complex OpenVPX compliant transceivers Mercury systems created OpenRFM™ to coordinate the integration of internal mechanical, RF, and digital elements. This framework successfully allowed the design to progress smoothly by minimizing integration issues. Additionally, OpenRFM yields a future-proof design since products can be easily updated without having to re-invent the interfaces.
To see OpenRFM™ in action, visit Mercury's website to learn about the ultra broadband, 3U OpenRFM™ transceiver.
Part 3 in the series is now available. Find out how Mercury applies proprietary technology to develop products that are both high-performance and extremely compact.